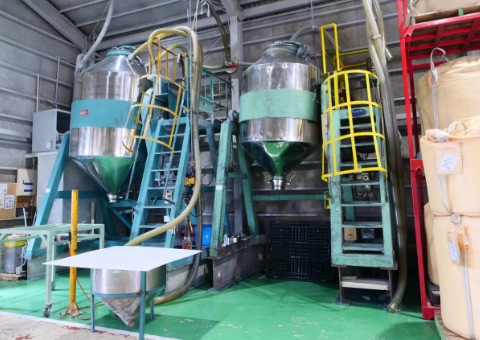
工程① タンブラー加工
タンブラー機で原材料となるペレットや粉砕などに顔料やマスターバッチ、各種添加剤を均一に混ぜ合わせます。数種類の材料をブレンドして、同一物性にすることが出来ます。 マスターバッチブレンドなどのブレンドのみの加工も承ります。
タンブラー加工担当・河瀬
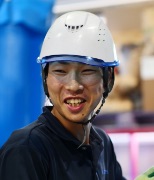
タンブラー加工を担当している河瀬です。タンブリングの工程で一番注意している事は、間違いのない物を仕込むという当たり前のことです。種類もそうですが、量も一つ間違えただけですべての材料がダメになってしまいます。品質にも大きく影響するブレンド作業ですので、何重にもチェックをしながら責任を持って毎日作業をしています。
工程② 押出加工
ブレンドした原材料を上部にあるホッパータンクより押出機に投入し溶融混錬します。混錬しながら押し出された樹脂はストランドといわれる太い糸のような状態で出てきます。ストランドは水槽で冷却し、ペレタイザー機で3mm程度にカットしペレット状にします。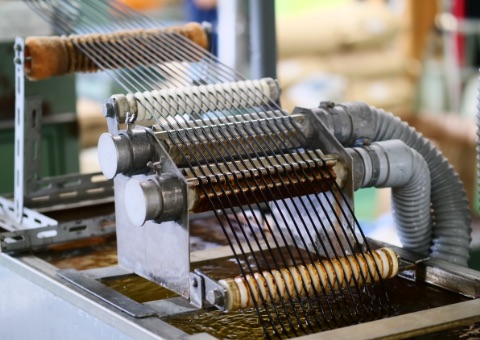
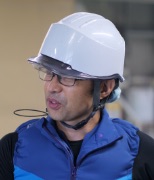
ルーダー加工を担当している服部です。樹脂によっては加工温度などシビアな管理が必要になります。その日の気温なども影響するので、見えないシリンダーの中をどのような状態で樹脂が通っているかを想像し考えながら最適な条件を導き出します。ただ加工するだけではなく、よりよい条件は無いか常に追求ながら、品質向上を念頭に日々作業することを心がけています。
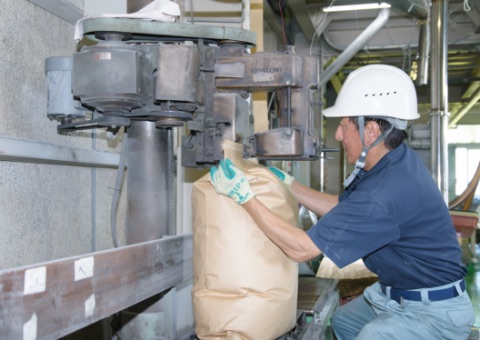
工程③ 選別、計量、袋詰め
カットされたペレットは選別機を通り、計量し袋詰めします。
ルーダー加工担当・岩津
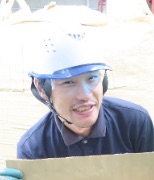
ルーダー加工を担当している岩津です。この工程は実際の製品の中身を確認できる最後の砦となります。ここでペレットの色や形、荷姿に異常がないことをしっかり確認をしなければ、直接お客様にご迷惑が掛かってしまいますので、細心の注意をしながら、自信を持って出荷できるよう作業をしています。
工程④ 検査
出来上がったペレットをお客様との取り決めに沿って、カラープレート、ダンベル片などを成形機で作成し各種検査を行います。 MFR、比重、衝撃強度(IZOD、シャルピー)、曲げ強度、引張強度、硬度、水分率、灰分率などを測定する検査機器を揃え、出荷する前に求められている品質を満たしていることを確認しています。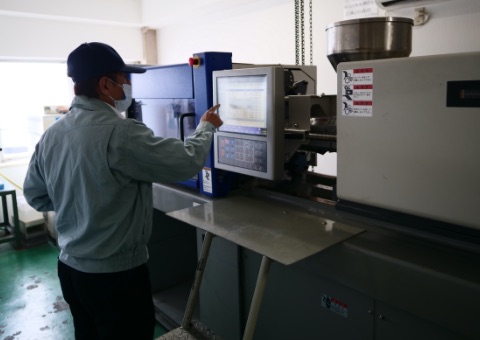
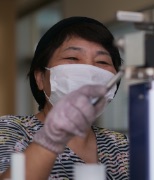
検査を担当している舘です。確実な品質管理をすることで、お客様に安心してご使用いただくのは勿論の事ですが、私たちもしっかりとした製品をを出荷しているという自信にもなりますので、正確な検査を心がけています。